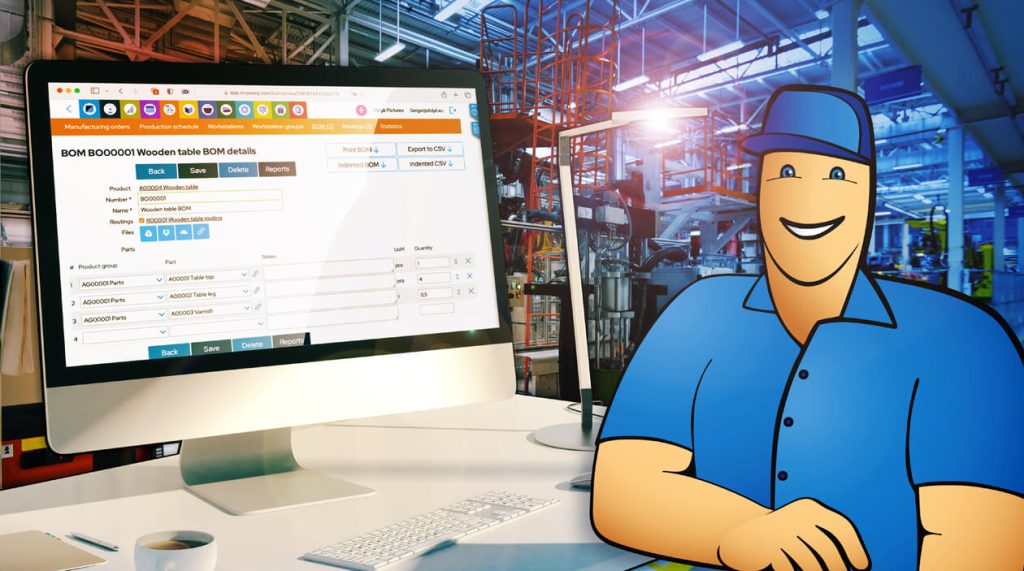
**Important Features of End Mills to Assess Before Purchasing**
End mills are crucial cutting tools utilized in milling tasks across sectors like aerospace, automotive, mold production, and general manufacturing. Choosing the appropriate end mill for a particular job can greatly influence machining efficiency, surface finish, and tool lifespan. Given the variety of options available, it is important to grasp the key features of end mills prior to making a purchase. This article examines the most significant characteristics of end mills to review for ensuring optimal performance and value.
—
### 1. **Material Makeup**
The composition of the end mill is critical in influencing its longevity, cutting efficiency, and compatibility with specific materials.
– **High-Speed Steel (HSS):** Delivers good toughness and is budget-friendly. Best for softer materials and general machining tasks.
– **Cobalt (M42):** Offers enhanced heat resistance compared to HSS, making it suitable for tougher materials.
– **Carbide:** Renowned for its hardness and wear resistance, carbide end mills excel in high-speed environments and when machining hard materials like stainless steel and titanium.
– **Ceramic and Diamond-Coated:** Intended for specialized tasks, such as machining composites or extremely hard substances.
—
### 2. **Type of Coating**
Coatings boost tool performance by minimizing friction, enhancing hardness, and increasing heat tolerance.
– **TiN (Titanium Nitride):** A general-purpose coating that prolongs tool life.
– **TiCN (Titanium Carbonitride):** Provides superior wear resistance, suitable for tougher materials.
– **TiAlN/AlTiN (Titanium Aluminum Nitride):** Optimized for high-temperature operations and dry machining.
– **DLC (Diamond-Like Carbon) and PCD (Polycrystalline Diamond):** Best for non-ferrous materials and abrasive composites.
—
### 3. **Flute Quantity**
Flutes are the channels that allow chip removal during cutting. The flute count influences chip evacuation, surface quality, and feed rates.
– **2-Flute End Mills:** Offer improved chip clearance, best for softer materials like aluminum.
– **3-Flute End Mills:** Provide a compromise between chip removal and surface finish quality.
– **4-Flute and Above:** Deliver enhanced surface finishes and strength, suitable for tougher materials but may necessitate slower feed rates to prevent clogging.
—
### 4. **Helix Angle**
The helix angle is defined by the angle between the tool’s centerline and the flute’s edge.
– **Low Helix (15°–30°):** Grants enhanced strength and is appropriate for tougher materials.
– **Medium Helix (30°–40°):** A versatile option for a variety of materials.
– **High Helix (40°–60°):** Optimizes chip removal and surface finish, ideal for softer materials like aluminum.
—
### 5. **End Configuration**
The design of the end mill’s cutting edge influences the type of cut it can produce.
– **Square End:** Used for slotting, profiling, and general milling tasks.
– **Ball Nose:** Ideal for 3D contouring and complex surfaces.
– **Corner Radius:** Provides additional strength and lessens chipping at the corners.
– **Chamfer End:** Utilized for beveling edges and deburring operations.
—
### 6. **Shank Design and Tool Holding**
The shank is the component of the tool that interfaces with the machine spindle. Compatibility with your tool holder is vital for precision and safety.
– **Straight Shank:** The most common type, compatible with standard collets.
– **Tapered Shank:** Enhances rigidity and alignment for specific applications.
– **Weldon Flat:** Ensures secure clamping in set-screw holders, minimizing slippage.
—
### 7. **Cutting Diameter and Length**
Selecting the proper diameter and length ensures the tool can reach the needed depth and fits the part geometry appropriately.
– **Cutting Diameter:** Must align with the width of the cut or slot.
– **Cutting Length:** Should be adequate for the cut depth without excessive overhang.
– **Overall Length:** Influences tool rigidity; longer tools may experience more deflection under load.
—
### 8. **Features for Specific Applications**
Certain end mills are tailored for particular materials or operations:
– **Aluminum-Specific End Mills:** Designed with polished flutes and high helix angles for improved chip evacuation.
– **Roughing End Mills:** Feature serrated edges for rapid material removal.
– **Finishing End Mills:** Crafted for high-precision and smooth surface finishes.
—
### Conclusion
Selecting the right end mill requires examining several crucial factors, including material, coating, flute count, helix angle, end configuration, and size. Grasping how these attributes interact with your specific machining application can result in enhanced performance, longer tool life, and greater cost-effectiveness. Always factor in the material being machined, the type of