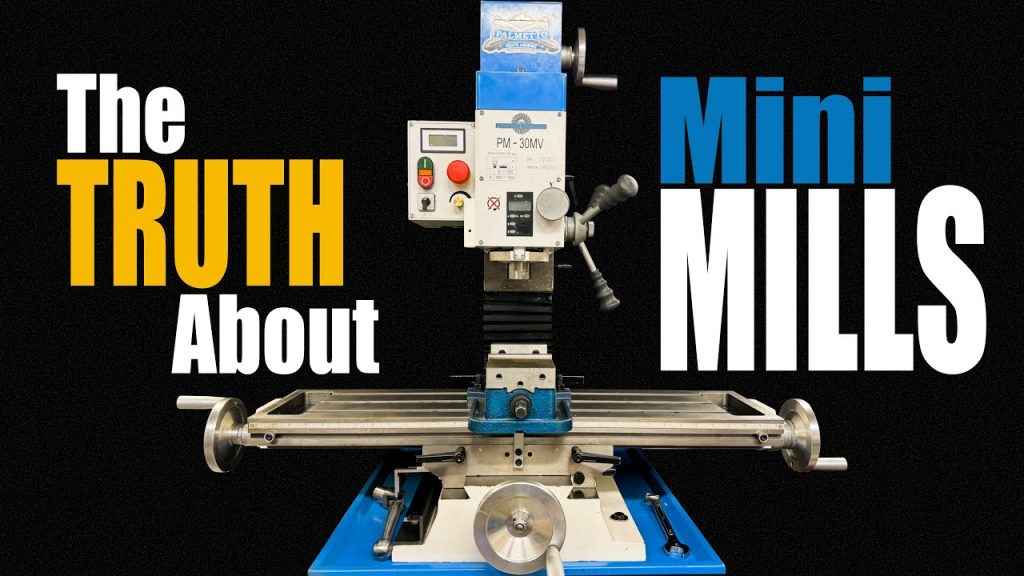
**Key End Mill Attributes to Consider Before Making a Purchase**
End mills are crucial cutting implements utilized in milling processes for material removal across industries such as aerospace, automotive, mold fabrication, and general manufacturing. Selecting the appropriate end mill can greatly influence machining effectiveness, surface quality, tool longevity, and overall production productivity. With a vast assortment of end mills on the market, it’s essential to assess several key attributes prior to making a purchase. This article highlights the most significant end mill features to contemplate to guarantee the best tool choice for your particular application.
—
### 1. **Material Composition**
The material of the end mill is crucial for its functionality and lifespan. Typical materials include:
– **High-Speed Steel (HSS):** Provides decent toughness and is appropriate for general milling, especially in softer materials.
– **Cobalt (M42):** Offers superior heat resistance and wear characteristics compared to HSS, perfect for tougher materials.
– **Carbide:** Renowned for its hardness and heat resistance, carbide end mills are suited for high-speed applications and the machining of hard materials.
– **Ceramic and Diamond-Coated:** Intended for specialized uses, such as machining exceptionally hard or abrasive materials.
**Tip:** For high-performance and extended tool life in challenging scenarios, carbide is frequently the top choice.
—
### 2. **Coating Type**
Tool coatings boost the performance of end mills by lowering friction, enhancing wear resistance, and facilitating heat dissipation. Common coatings include:
– **TiN (Titanium Nitride):** General-purpose coating that boosts tool hardness and oxidation resistance.
– **TiCN (Titanium Carbonitride):** Provides improved wear resistance compared to TiN, suitable for tougher materials.
– **TiAlN/AlTiN (Titanium Aluminum Nitride):** Outstanding for high-speed and high-temperature applications; ideal for dry machining.
– **DLC (Diamond-Like Carbon):** Minimizes friction and is suitable for non-ferrous materials like aluminum and plastics.
**Tip:** Align the coating with your workpiece material and machining conditions for the best outcomes.
—
### 3. **Number of Flutes**
Flutes are the grooves that facilitate chip removal during cutting. The flute count influences chip evacuation, surface finish, and feed rates.
– **2-Flute:** Best suited for softer materials such as aluminum; allows improved chip evacuation.
– **3-Flute:** Provides a balance between chip clearance and strength; suitable for aluminum and plastics.
– **4-Flute and Above:** Ideal for tougher materials and finishing tasks; yields a finer surface finish.
**Tip:** Opt for fewer flutes when roughing and with materials that create large chips, and more flutes for finishing and harder materials.
—
### 4. **Helix Angle**
The helix angle is the angle between the tool’s centerline and the edge of the flute. It influences cutting action, chip extraction, and surface finish.
– **Low Helix (20°–30°):** Delivers greater strength and is appropriate for tougher materials.
– **Medium Helix (35°–40°):** Provides a well-rounded balance of strength and chip evacuation.
– **High Helix (45°+):** Boosts chip evacuation and is perfect for softer materials like aluminum.
**Tip:** Select a helix angle based on the material and desired finish, as higher angles reduce cutting forces and enhance surface quality.
—
### 5. **End Geometry**
The configuration of the end mill’s cutting end determines its appropriateness for various operations.
– **Square End:** Suitable for milling flat surfaces, slots, and pockets.
– **Ball Nose:** Perfect for 3D contouring and intricate surface machining.
– **Corner Radius:** Provides added strength at the corners, minimizing chipping and increasing tool longevity.
– **Chamfer End:** Utilized for beveling edges and deburring tasks.
**Tip:** Tailor the end geometry to your application to optimize tool performance and part quality.
—
### 6. **Cutting Diameter and Length**
The cutting diameter and overall length of the end mill must align with the demands of your machining setup.
– **Cutting Diameter:** Determines the width of the cut and must correspond with the machine’s spindle and collet.
– **Cutting Length:** Influences how deeply the tool can cut in one pass.
– **Overall Length:** Affects tool stability; longer tools are more susceptible to deflection.
**Tip:** Employ the shortest tool feasible for the task to reduce deflection and enhance precision.
—
### 7. **Shank Type and Size**
The shank is the part of the end mill that fits into the tool holder. Common varieties include:
– **Straight Shank:** The most prevalent type and compatible with standard collets.
– **Weldon Flat Shank:** Features a flat section for set screws to prevent tool slippage.
– **Tapered Shank:** Designed for specific applications that require added rigidity.
**Tip:** Confirm that